Capabilities
High Technology Center
Advanced solutions in the aerospace, energy, and automotive sectors.
HTC provides advanced technological solutions through specialized expertise and state-of-the-art facilities. Leveraging these cutting-edge technologies and our nearly two decades of experience, we are equipped to tackle the most complex challenges and implement advanced processes that optimize performance and meet customized needs effectively.
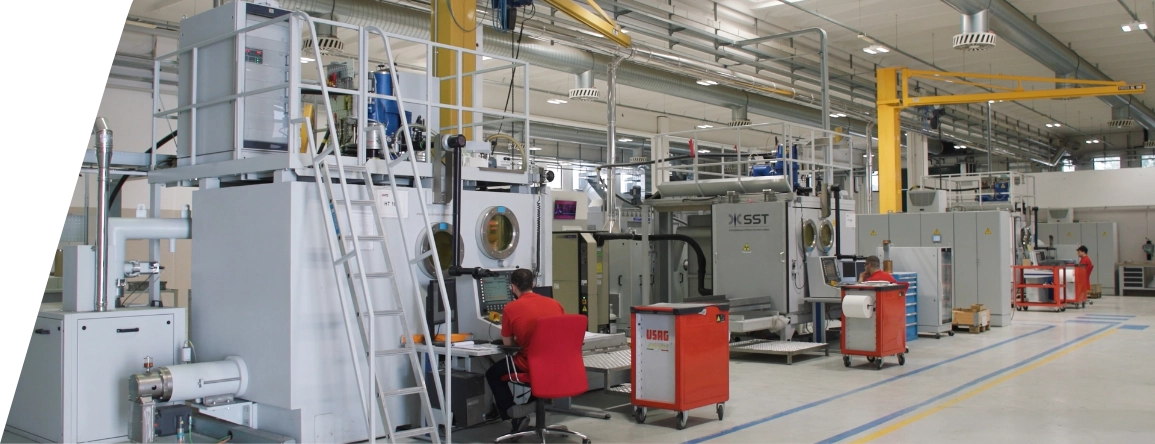
Capabilities
HTC offers a range of capabilities to meet various industrial needs. Our expertise in electron beam welding (EBW) allows us to produce precise, durable joints for critical components. We use high-vacuum furnaces for heat treatments and brazing, ensuring rigorous control over conditions and high-quality results. Our plasma and HVOF (High-Velocity Oxygen Fuel) coating processes provide advanced surface protection, enhancing component durability and performance. Additionally, our grinding capabilities ensure flawless surface finishes.
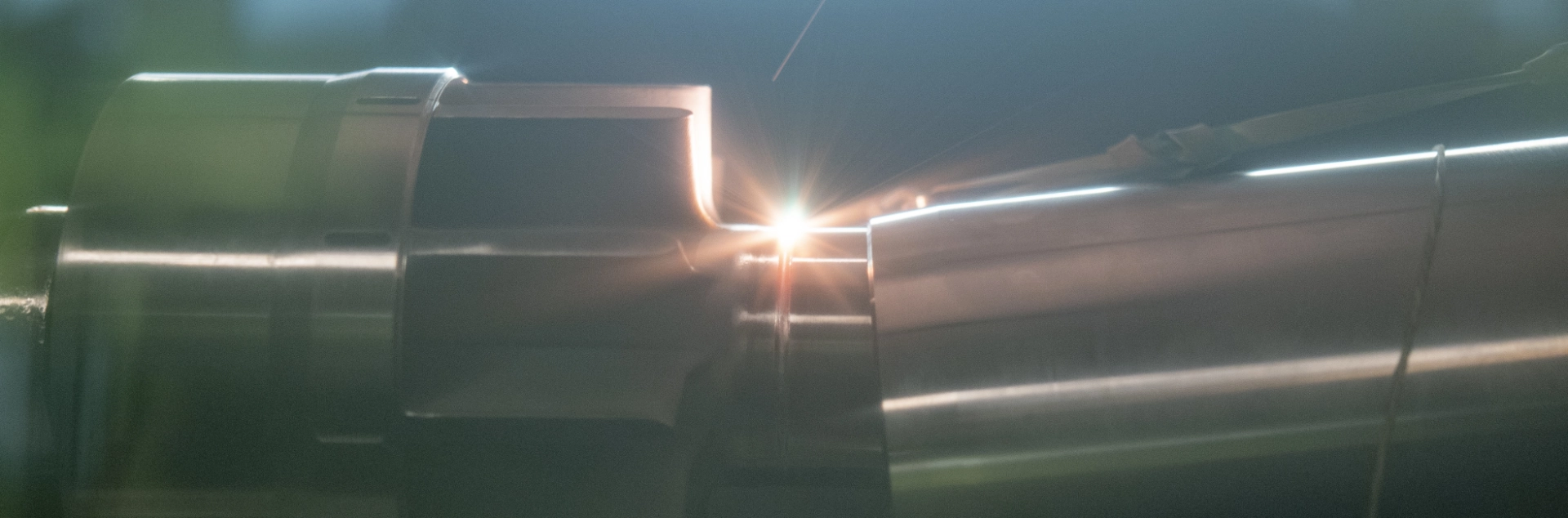
Electron Beam Welding (EBW)
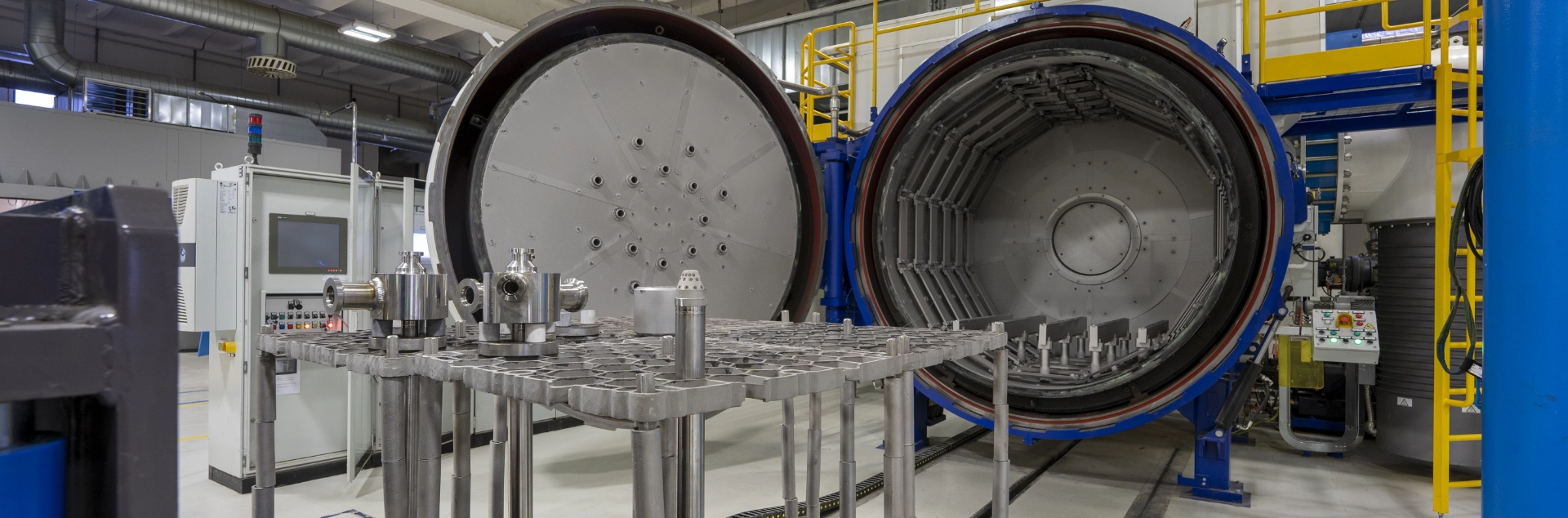
Heat treatments
Heat treatments and brazing are critical processes for achieving quality, durability, and reliability required in metal components. HTC employs high-vacuum furnaces with horizontal loading and pressurized gas quenching (Argon / Nitrogen) to perform a wide range of heat treatments on materials commonly used in advanced industrial sectors, such as aerospace and energy.
The heat treatments performed include solution annealing and aging of nickel-based alloys (superalloys), precipitation hardening of PH steels, quenching and tempering of martensitic steels, stress relieving of austenitic stainless steels, and stress relieving of titanium alloys.
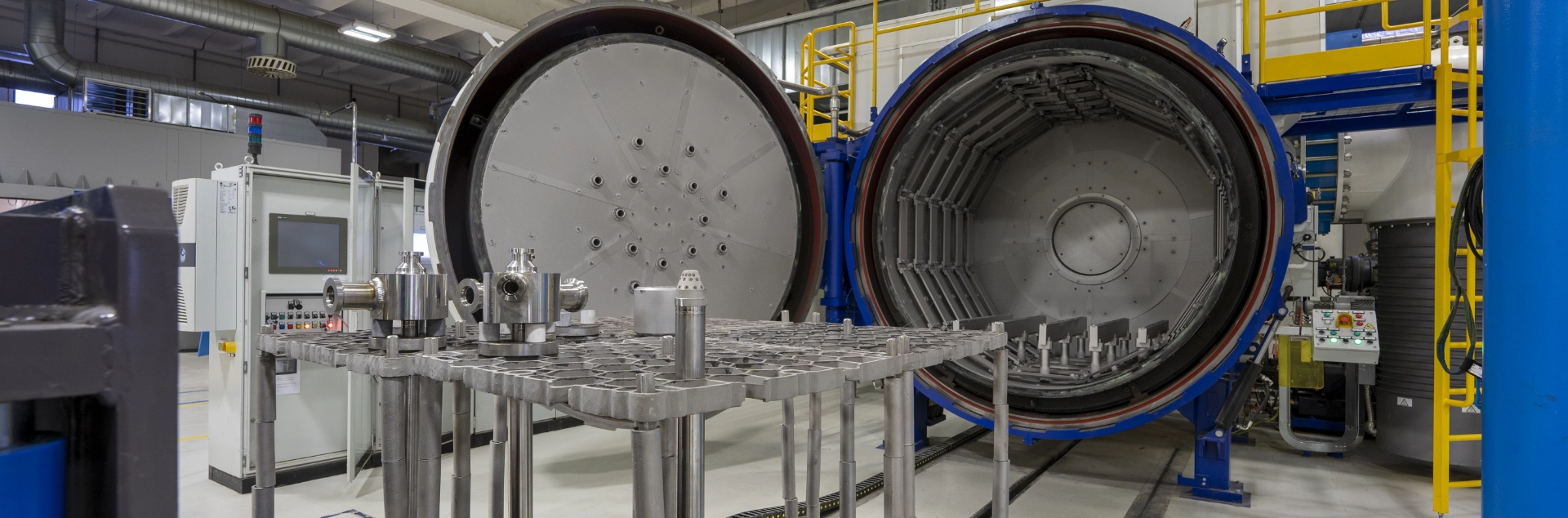
Brazing
Brazing is also part of these processes, providing strong and precise joints between metals through the use of an external filler material (brazing alloy) with a melting point lower than that of the base materials. Vacuum brazing is especially suited for applications in sensitive environments, such as aerospace and energy industries, as the absence of oxygen and other gas contamination ensures clean and robust joints.
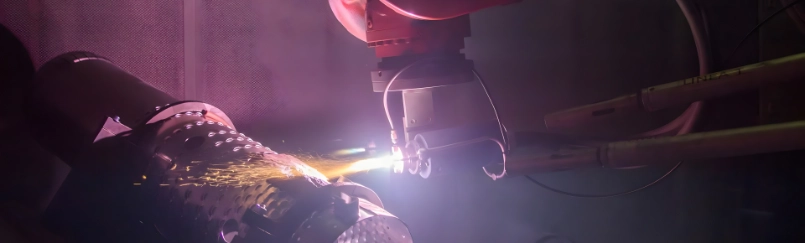
Air Plasma Spray Coating
The Plasma coating (APS, Air Plasma Spray) is a thermal spraying process ideal for applying advanced protective layers to a variety of components that must withstand harsh working conditions, such as those in gas turbines and engines, in the aerospace and automotive industries.
This automated process allows the application of hardening coatings, abradable coatings, or thermal barrier coatings (TBC) on a wide range of metallic materials, improving the components’ wear resistance, corrosion resistance, fatigue resistance, and high-temperature durability.

HVOF coatings
The High-Velocity Oxy-Fuel (HVOF) coating process is a thermal spraying technique used to apply high-quality protective coatings to components operating under extreme conditions, such as those in gas turbines, engines and high-performance applications. This process is characterized by the high velocity at which the coating material is projected into the surface, resulting in a dense coating with excellent adhesion.
HVOF coatings are an effective and versatile solution to enhance the durability, reliability and performance of components exposed to wear, corrosion, and high temperatures. Coatings made with pure chrome, chromium carbides or tungsten carbides can serve as an alternative to hard chrome plating, providing superior protection against wear and corrosion.

Grinding
Grinding is a machining process performed to enhance the dimensional accuracy and surface quality of coatings applied using Plasma and HVOF spraying technologies. It is essential in cases where components must meet precise dimensional tolerances or require smooth, well-defined surfaces to optimize performance. Grinding of coatings is particularly valuable in advanced industrial applications, such as the automotive and aerospace sectors, where the durability and reliability of components are critical.
HTC is equipped to perform grinding on both external and internal surfaces.